Seit der Erfindung des 3D-Drucks gilt Additive Manufacturing als Schlüsseltechnologie vor allem für die Erzeugung komplexer Geometrien und Leichtbaukomponenten. Auch bei Pankl werden seit einigen Jahren Bauteile mittels metallischem 3D-Druck hergestellt. Weil wir vor allem im Racing- und High Performance-Bereich großes Potenzial sehen, versuchen wir bei Pankl gemeinsam mit Partnern dieses Fertigungsverfahren mit neuen Methoden, wie zum Beispiel Smart Fusion, in der Industrie zu etablieren.
Additive Manufacturing, Laser-Sintern und Titanpulver: So funktioniert die Fertigungstechnologie
Beim Additive Manufacturing entsteht auf Basis von digitalen 3D-Konstruktionsdaten ein Bauteil, welches nicht aus einem festen Block zerspant, sondern aus Metallpulver gefertigt wird. Eine Schicht des Metallpulvers wird auf eine Bauplatte aufgetragen und mit einem leistungsstarken Laser an den vorgegebenen Stellen in die gewünschte Form geschmolzen. Dieser Vorgang wiederholt sich Schicht für Schicht, bis das Bauteil vollständig gedruckt ist. Je nach Komplexität und Größe kann der ganze Vorgang mehrere Tage dauern. Umgangssprachlich wird das Verfahren deshalb auch als „metallischer 3D-Druck“ bezeichnet.
Um die Bauteile während des Druckens in Form zu halten, werden zusätzlich Stützstrukturen, sogenannte Supports, mitgedruckt. Diese dienen dazu, die Objekte während der Herstellung in Form zu halten und überhängende Bereiche vor Überhitzung zu schützen. Diese Supports werden bereits in der Designphase berücksichtigt und müssen nach dem Druck manuell entfernt werden. An der Außenseite der Bauteile ist das kein Problem, die große Herausforderung liegt oft im Innenbereich, der nicht so leicht zugänglich ist. Hinzu kommt, dass das entfernte Material der Stützstrukturen nicht wiederverwertet werden kann.
Um die Fertigungskosten weiter zu reduzieren und damit die Technologie weiter zu verbreiten, muss eine Möglichkeit gefunden werden, Bauteile in diesen Überhang zu fertigen, ohne eine Vielzahl von Stützen „mitdrucken“ zu müssen. Hier setzt Smart Fusion an.
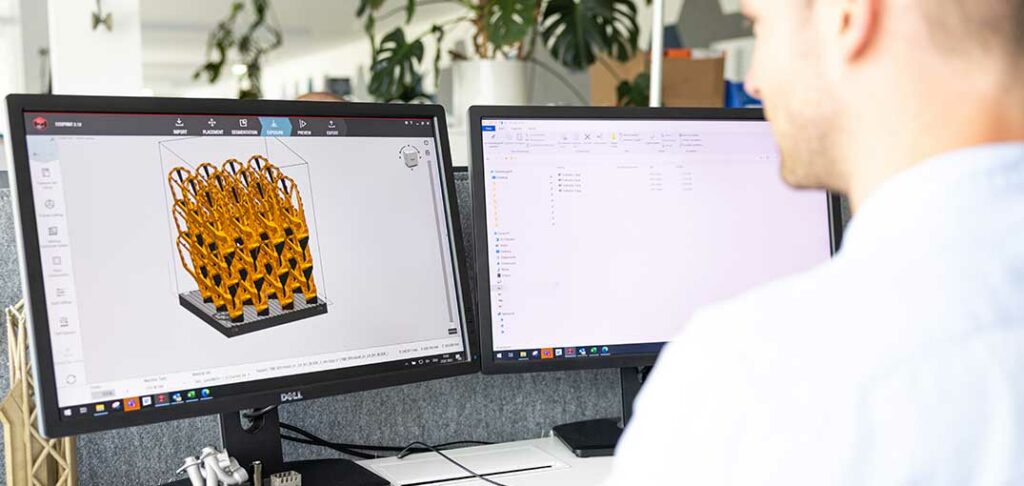
Was bedeutet Smart Fusion im AM-Bereich?
Während der additiven Fertigung wird der Laser mit einer bestimmten Energie auf das Metallpulver gerichtet. Diese Energie wird von drei Faktoren bestimmt: Der Laserleistung, der Lasergeschwindigkeit und dem Abstand zwischen zwei Laservektoren. In der Regel wird diese Energie über den gesamten Fertigungsprozess nicht geregelt, d.h. unabhängig von der Geometrie oder anderen Faktoren wie Wandstärke, Überhangwinkel etc. wird überall die gleiche Energie eingesetzt. Das bedeutet natürlich, dass verschiedene Bereiche stärker überhitzt werden als andere, die z.B. konstruktionsbedingt dickere Wandstärken aufweisen.
Um dies zu überwachen, wurde in der Druckkammer der EOS-Druckmaschinen eine optische Tomografiekamera angebracht, eine Art Wärmebildkamera, die während des Druckvorgangs sehr detaillierte Wärmebilder aufnehmen kann. Jedem Pixel dieser Aufnahme wird dabei ein sogenannter Grey Value (GV) und eine entsprechende Farbe zugeordnet – Rot steht für hohe, blau für die niedrigsten GV-Werte. Die dunkelroten Pixel in der Abbildung deuten auf eine Überhitzung hin.

Mittels dem Smart Fusion System wird die Laserleistung in Echtzeit auf Basis der Grey Values geregelt, was bedeutet, dass wenn die Grey Value höher als der eigenstellte Zielwert ist, genau in diesem Bereich die Laserleistung entsprechend reduziert wird und so keine Überhitzung stattfindet.
Die großen Vorteile von Smart Fusion in der additiven Fertigung liegen auf der Hand: Material- und Ressourceneinsparungen bei den Trägern sind ein wesentlicher Vorteil. Auch die Zeitersparnis bei der Fertigung ist erheblich. Nicht nur, weil das Bedrucken des Trägers weniger Laserzeit benötigt, sondern auch weil in der Nacharbeit wesentlich weniger Supports zu entfernen sind und somit die Durchlaufzeit reduziert, sowie Kapazität freigeschaufelt werden können.
Ein weiteres bemerkenswertes Merkmal der Smart Fusion-Technologie ist die Tatsache, dass die Anzahl der Bauteile pro Druckvorgang deutlich erhöht werden kann. Dies wird durch das Drucken von Teilen mit weniger Stützstrukturen erreicht, wodurch weniger Platz benötigt wird. Dies ermöglicht eine bessere Verschachtelung und Anordnung der Teile. In der Praxis bedeutet dies, dass mehrere Teile gleichzeitig und effizienter hergestellt werden können. Diese Optimierung des Produktionsprozesses spart nicht nur Zeit, sondern senkt auch die Kosten. Die Erhöhung der Stückzahl pro Druckvorgang ist ein wesentlicher Vorteil, der die Effizienz und Wirtschaftlichkeit dieser innovativen Fertigungsmethode unterstreicht.
Das Pankl Additive Competence Center
Das Pankl Additive Manufacturing Competence Center hat bereits eine Vielzahl von Komponenten erfolgreich gefertigt. Ein herausragendes Beispiel im Motorsport ist der Top Frame des Aeroscreens, der seit mehreren Jahren in der IndyCar-Rennserie eingesetzt wird.
Darüber hinaus werden im Additive Manufacturing Competence Center regelmäßig KTM-Fußrasten in hohen Stückzahlen gefertigt. Aufgrund der Geometrie, der Fertigungszeit und der Kosten setzt KTM hier auf den metallischen 3D-Druck. Seit einiger Zeit wird für diesen wiederkehrenden Auftrag auch Smart Fusion eingesetzt. Durch den Einsatz einer optischen Tomographiekamera in Kombination mit vordefinierten Grauwerten konnte nicht nur die Stückzahl innerhalb eines Druckauftrages vervierfacht, sondern auch die Nachbearbeitungszeit drastisch reduziert werden. Diese Effizienzsteigerung und der geringere Materialeinsatz sind die enormen Vorteile, die Smart Fusion für die Produktion mit sich bringt. Das Pankl Additive Manufacturing Competence Center nutzt diese Vorteile, um innovative Lösungen zu entwickeln und die Effizienz der additiven Fertigung weiter zu steigern.
Herausforderungen und Chancen im Bereich Smart Fusion
Smart Fusion bietet viele Möglichkeiten für die additive Fertigung. Die enormen Effizienzvorteile können für die Verbreitung der Technologie von großem Vorteil sein. Um Smart Fusion nicht nur projektbezogen, sondern als dauerhafte Lösung einzusetzen, müssen auch nachgelagerte Prozesse wie das Qualitätsmanagement berücksichtigt werden. Bei neuen Aufträgen ist es hier besonders wichtig, die Bauteile nicht nur während des Produktionsprozesses, sondern auch in der Nachbearbeitung und Qualitätssicherung zu analysieren, um die Leistungsfähigkeit der Bauteile umfassend zu gewährleisten.
Denn bei erfolgreichen Projekten – wie zum Beispiel der KTM-Fußraste – müssen die Produktionsparameter im additiven Fertigungsprozess eingefroren und bei Folgeaufträgen einfach abgerufen werden. Und genau solche Prozesse beschleunigen die oft notwendigen Zertifizierungen, die wir als Unternehmen für unsere namhaften Kunden benötigen.
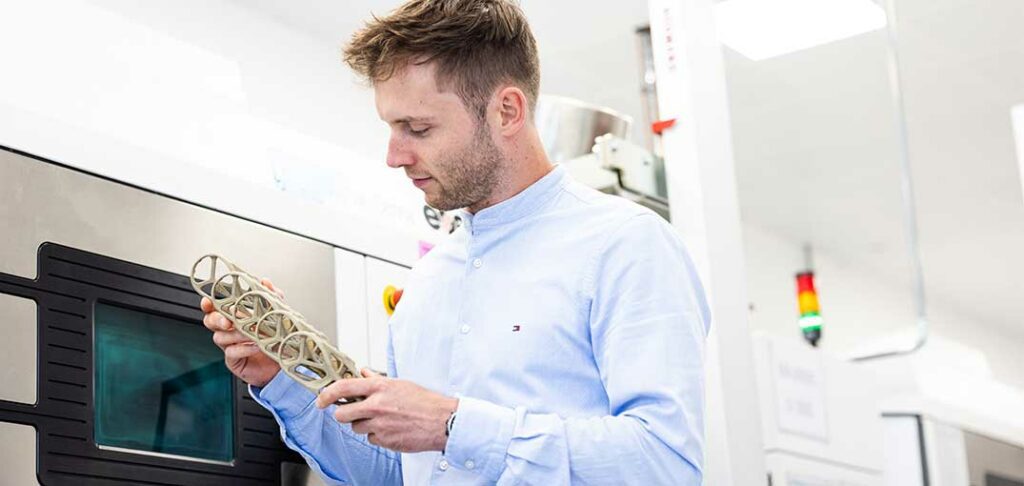
Smart Fusion ist zweifellos ein Game Changer im Bereich der additiven Fertigung. Durch die Reduktion von Supportstrukturen und die damit verbundene Erhöhung der Stückzahl pro Job eröffnet das Verfahren großartige Möglichkeiten, den Weg zur Serienproduktion zu ebnen. In den vergangenen Monaten haben wir bei Pankl mit EOS zusammengearbeitet, um das enorme Potenzial, insbesondere für die Serienfertigung, zu erforschen. Mit unserer hauseigenen Fertigungskette sind wir zudem in der Lage, Optimierungspotenziale in der Nachbearbeitung und Materialprüfung zu identifizieren und diese in neue Projekte umzusetzen, ohne großen Aufwand zu betreiben. Diese enge und abteilungsübergreifende Zusammenarbeit ermöglicht es uns, die Vorteile von Smart Fusion voll auszuschöpfen und innovative Lösungen für zukünftige Herausforderungen in der Produktion zu entwickeln.