Die Formel-1-Saison ist bereits in vollem Gange, und mit ihr wächst auch das Interesse an der neuesten Staffel von Netflix‘ „Drive to Survive“. Doch was viele Fans nicht wissen: Additive Manufacturing hat mittlerweile Einzug in die Königsklasse des Motorsports gehalten. Was vor zehn Jahren noch undenkbar war, ist heute Standard auf den Rennstrecken der Welt.
Additive Manufacturing in der Formel 1
Die additive Fertigung hat einige Zeit gebraucht, um sich im Hochleistungsmotorsport zu etablieren. Die COVID-Pandemie, Regulation Freezes und Cost Caps haben zunächst den Fortschritt ausgebremst. Der Motorsport stellt höchste Qualitätsansprüche, Ausfälle durch Materialversagen oder Fahrzeuge, die nicht ins Ziel bei einem Rennen kommen, sind nahezu ausgeschlossen. Die Entwicklung der additiven Fertigung hat entscheidend dazu beigetragen, diese Standards zu erfüllen.
Pankl hat über Jahre hinweg intensiv in den Ausbau und die Forschung und Entwicklung investiert, insbesondere im Bereich des Leichtbaus. Heute kommen additiv gefertigte Bauteile in vielen Bereichen der Formel 1 zum Einsatz. Besonders im Bereich der Aerodynamik sind additiv gefertigte Flügelkonstruktionen eine bevorzugte Lösung, da sie schnell modifiziert und an die neuesten Entwicklungen angepasst werden können. Doch auch hydraulische Komponenten und Motorteile profitieren von der Technologie, insbesondere durch Gewichtsersparnis und optimierte Strömungseigenschaften.
Sorgt für die Sicherheit: Der Überrollbügel
Ein sehr wichtig additiv gefertigtes Bauteil ist der Roll Hoop, der Überrollbügel eines Formel-1-Autos. Dieses sicherheitskritische Teil sitzt oberhalb des Fahrers, am höchsten Punkt des Fahrzeugs und übernimmt zwei essenzielle Aufgaben. Zum einen definiert es den Lufteinlass für den Motor, zum anderen schützt es den Fahrer im Falle eines Unfalls, insbesondere bei einem Überschlag. Entscheidend für die Schutzwirkung ist, dass der Helm des Fahrers stets unter einer festgelegten Sicherheitslinie bleibt – einer imaginären Verbindung zwischen der vorderen Halo-Befestigung und einem definierten Punkt am Fahrzeugheck.
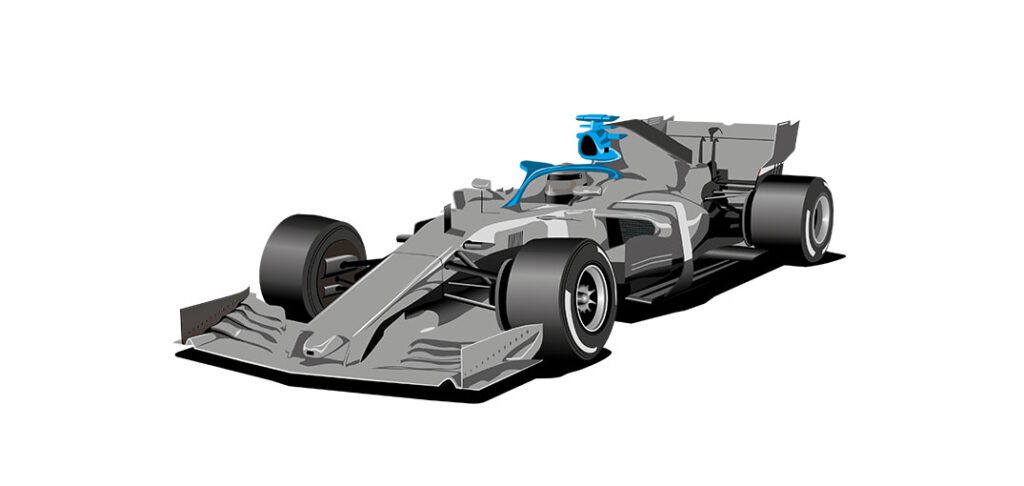
Dank additiver Fertigung können Überrollbügel mit komplexen, hochoptimierten Strukturen gefertigt werden, die maximale Stabilität bei minimalem Gewicht bieten. Der Einsatz von Carbonstrukturen und Titanbauteilen sorgt für eine ideale Kombination aus Festigkeit und Leichtbau. Zudem ermöglicht der 3D-Druck eine schnelle Anpassung an neue Designanforderungen und aerodynamische Optimierungen. Die Entwicklung erfolgt parallel zum Chassis-Design und durchläuft mehrere Iterationen, um höchste Sicherheits- und Leistungsanforderungen zu erfüllen.
Additive Fertigung: Schlüsseltechnologie der Zukunft?
Pankl beschäftigt sich seit mehr als zehn Jahren mit der additiven Fertigung. „Wir sehen diese Technologie als zukunftsweisend, jedoch nicht als Ersatz, sondern als Ergänzung zu konventionellen Fertigungsmethoden. Unsere Strategie besteht darin, die additive Fertigung gezielt dort einzusetzen, wo sie den größten Nutzen bringt“, so Stefan Seidel, CTO Pankl Racing Systems AG.
Ein entscheidender Faktor für den Erfolg dieser Technologie liegt in der durchgängigen Qualitätssicherung. Pankl arbeitet eng mit Partnern wie EOS oder voestalpine Böhler Edelstahl zusammen, um neue Pulver zu entwickeln und deren Qualität, Konsistenz und Eigenschaften zu optimieren. Zudem wurde vor Jahren in die Hot Isostatic Pressing (HIP) investiert, eine Technologie, die die Ermüdungseigenschaften von Bauteilen signifikant verbessert und damit für noch höhere Sicherheit sorgt.
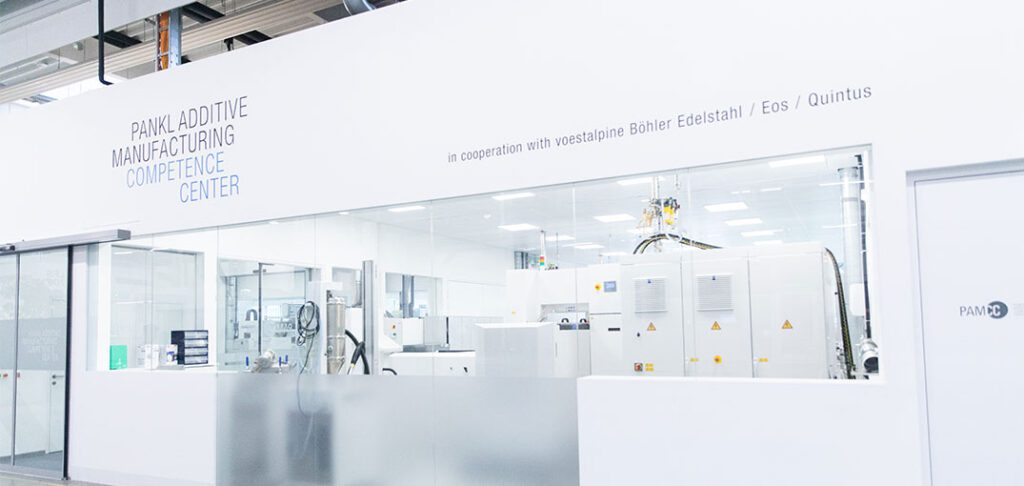
„Durch unsere geschlossene Wertschöpfungskette – von der Pulverentwicklung über die Fertigung bis hin zur Endkontrolle – schaffen wir es, die additive Fertigung in neue Anwendungen zu bringen und die Performance von Rennsportkomponenten auf ein neues Level zu heben“, so Seidel.